ITEA4 ASIMOV Project
Script error: No such module "Draft topics".
Script error: No such module "AfC topic".
The ASIMOV project (AI training using Simulated Instruments for Machine Optimization and Verification) is a collaborative research project running under the ITEA4 programme within the Eureka framework. It was proposed under the Eureka AI call 2020.[1].
The project started on June 1, 2021 and it will run until May 31, 2024.
The ASIMOV project will research methods and technology to train AI Algorithms for configuring and optimizing (calibrating) Cyber-Physical Systems (CPSs). In order to reduce the amount of data and time needed to train these AI algorithms, the project will research the creation of physically realistic Digital Twins that can be used as simulations of the CPSs for the training.

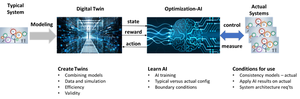
Consortium[edit]
The project is executed by a consortium of partners from Finland (funding decision pending - partners will be added later), Germany and The Netherlands:
- AVL Deutschland GmbH
- CQM
- Eindhoven University of Technology,
- LiangDao GmbH
- NorCom GmbH & Co.KGaA
- OFFIS (until December 31, 2021)/DLR (Institut Systems Engineering für zukünftige Mobilität, per January 1, 2022)
- RA Consulting GmbH
- Thermo Fisher Scientific,
- TrainGraphics GmbH
- TNO (ESI)
Industrial Use Cases/Proofs of Concept[edit]
The project will develop the Digital Twin-based AI-training technology using industry use cases provided by the consortium partners:
- electron microscopes
- unmanned utility vehicles
- a use case provided by the Finnish sub-consortium will be added when the funding is granted in Finland.
Research Challenges[edit]
The project has the ambition to deliver innovations in the following areas:
- methods and tools for creating digital twins of systems to simulate realistic system behavior
- methods and tools for training an AI using the digital twin to find optimal system settings
- methods and tools for verifying the validity of the digital twin for training the AI
- methods and system architectures to use the trained AI to perform the tuning and calibration tasks on actual machine configurations
The research will lead to AI-based software that autonomously performs system optimization tasks during manufacturing, installation, and system usage. Proof of concepts will be provided in three different industrial system domains for which optimization is crucial for system performance.
Digital Twinning[edit]
Digital twins are up-to-date virtual representations of actual Cyber-Physical Systems (CPSs) in operation. By integrating physical, software and hardware models, internet of things, artificial intelligence and analytics, digital twins provide simulation models that update and change as their cyber-physical counterparts change. Introduced in 2003[2], the concept is finding its way into industry prompted by recent technological advances[3]. Digital twins allow companies to have a complete digital footprint of their products from design and development phases to the end of the product life cycle[4]. This can be leveraged in multiple ways, which include operations optimization, predictive maintenance, anomaly detection and fault isolation.
Digital twins have been used in many industrial applications, such as heat transfer modelling, solidification modelling, property prediction, residual stress modelling, and distortion modelling[5], 3-D printing processes, high-fidelity generalized method of cells for composite materials simulation to enhance the efficiency of data processing in aerospace digital twins[6], milling machines, where sensor data were used to monitor machining operations and predict surface roughness[7], offshore drilling[8], offshore wind turbines[9][10], space structures[11], nuclear fusion[12], wind farms[13], power systems[14] and many more. Key industrial players such as General Electric and Bosch are investing strongly in this novel concept.[15][16]
Much of the utility of a digital twin comes from its ability to predict future system behaviour. In order to achieve this, reliable models of underlying parts of the system, often of a different nature (chemical, electrical, mechanical, software) are crucial. These models can be obtained by white-box first principle modelling, i.e. physical modelling of the processes involved, data-driven methods, where input-output relations of data entering and exiting the CPS are modelled, or their combination.
Important challenges in this context include:
- How to combine multi-physics processes, such as chemical, mechanical, electrical, processes and cyber processes, including software and communication, of very different natures and often operating at different length and time scales? How to deal with the heterogeneity of the models, the modelling languages and tools they are formulated in?
- How to tame the complexity and how to deal with the large scale of real CPSs, such as electron microscopes, self-driving cars and their environment, amongst many others? Open questions in common digital twin approaches include how to keep model complexity low enough to enable fast real-time simulation/data generation for training but high enough to be realistic? as well as what model reduction techniques are valid to achieve this? i.e., to find a good trade-off between accuracy , validity and representativeness of the digital twin and its complexity, such that the analysis does not become too costly and still delivers meaningful results with predictable uncertainty;
- How to ensure that, while the digital twin is ideally delivered with the product at the start of its operational life, it stays meaningful over the life-cycle of the product or process at hand?[17]
Further open questions include uncertainty management and the quantification of trust of the digital twin.[18] A basis of trust is the validity or representativeness of the digital twin. Model validation is usually defined to mean “substantiation that a computerized model within its domain of applicability possesses a satisfactory range of accuracy consistent with the intended application of the model.”[19] As virtual counterparts of (cyber-) physical systems, digital twins face very similar (or, rather, even harder) validation challenges as other computerized models.
AI-Training[edit]
The applicability of Artificial Intelligence (AI) and Machine Learning (ML) techniques to real-world complex systems is often limited by the huge amount of good training data required to sufficiently learn the system's dynamics or its behavior.[20] [21] With an accurate virtual environment provided by a digital twin, it is possible to simulate many repetitions and scenarios to generate huge amounts of training data. This enables the simulating potential real-world conditions that would otherwise very rarely occur. Some approaches use human knowledge to shape the distribution of conditions such that rare events occur more often.[22] These techniques automatically determine the simulation parameters such that the performance of the trained model on synthesized data is maximized.[23]
Obtaining labelled training data through a digital twin is part of the popular supervised learning paradigm. However, in many cases, it is not possible to automatically assign the correct labels to decisions. Reinforcement Learning (RL)[24], which relies on data patterns or delayed decision rewards, is an alternative training paradigm that reduces the labelling problem. In particular, RL is a key enabler for smart decision-making systems.[25] For instance, in [26] the authors illustrate how RL can support operation and maintenance of power grid applications. A key challenge for trial-and-error based RL algorithms is data efficiency. The RL algorithms often require a tremendous number of system interactions, which is impractical in many real-world applications. For instance, the success of AlphaGo[27] is mainly due to the fact that simulations could be taken offline and performed faster than real time, otherwise the amount of data from training on real games would be intractable. The data inefficiency of RL training approaches makes that complex real-world control systems without task-specific priors are too challenging; think, for instance, of robot walking, e.g. the Boston Dynamics Robot Dog (Spot), or the image forming operation modes of an Electron Microscope. Recent works provide some directions to increase the data efficiency of RL by learning models of the underlying system dynamics.[28]
The following research questions have been identified:
- How to combine Digital Twins with Reinforcement Learning such that the found solution is applicable to the real-world problem?
- How to enable improvements in the data efficiency and stability of Reinforcement Learning such that solutions are obtained in reasonable time?
- How to develop efficient distributed simulation approaches such that the simulation of multiple Digital Twins can be performed in a scalable way?
Publications from the ASIMOV-project[edit]
References[edit]
- ↑ "AI Call 2020 - ITEA projects - Diverse and promising innovations improving AI" (PDF). ITEA Magazine. ITEA (38): 28–31. March 2021.
- ↑ Grieves, Michael (March 2015). Digital Twin : Manufacturing Excellence through Virtual Factory Replication. Search this book on
- ↑ Tao, F.; Zhang, H.; Ne, A.Y.C (April 2019). "Digital Twin in Industry: State-of-the-Art". IEEE Transactions on Industrial Informatics. 15 (4): 2405–2415. doi:10.1109/TII.2018.2873186. Unknown parameter
|s2cid=
ignored (help) - ↑ Parrott, Aaron; Warshaw, Lane (12 May 2017). "Industry 4.0 and the digital twin - Manufacturing meets its match" (PDF). Deloitte. Deloitte University Press.
- ↑ DebRoy, T.; Zhang, W.; Turner, J.; Babu, S.S. (June 2017). "Building digital twins of 3D printing machines". Scripta Mater. 135: 119–124. doi:10.1016/j.scriptamat.2016.12.005.
- ↑ Ricks, T.M.; Lacy, E.; Pineda, E.J.; Bednarcyk, B.A.; Arnold, S.M. (2015). "Computationally efficient solution of the high-fidelity generalized method of cells micromechanics relations". Proc. 30th Tech. Conf. Amer. Soc. Composites. Unknown parameter
|s2cid=
ignored (help) - ↑ Cai, Yi; Starly, Binil; Cohen, Paul; Lee, Yuan-Shin (December 2017). "Sensor Data and Information Fusion to Construct Digital-twins Virtual Machine Tools for Cyber-physical Manufacturing". Procedia Manufacturing. 10: 1031–1042. doi:10.1016/j.promfg.2017.07.094.
- ↑ Sharma, Partha; Hamedifar, Hamed; Brown, Aaron; Green, Richard (May 2017). "The Dawn of the New Age of the Industrial Internet and How it can Radically Transform the Offshore Oil and Gas Industry". Offshore Technology Conference. doi:10.4043/27638-MS.
- ↑ Sivalingam, Krishnamoorthi; Sepulveda, Marco; Spring, Mark; Davies, Peter (2018). "A Review and Methodology Development for Remaining Useful Life Prediction of Offshore Fixed and Floating Wind turbine Power Converter with Digital Twin Technology Perspective". 2nd International Conference on Green Energy and Applications (ICGEA): 197–204. doi:10.1109/ICGEA.2018.8356292. hdl:1842/36085. ISBN 978-1-5386-5234-3. Unknown parameter
|s2cid=
ignored (help) - ↑ Tygesen, U.T.; Jepsen, Michael S.; Vestermark, Jonas; Dollerup, Niels; Pedersen, A. (17 June 2018). "The True Digital Twin Concept for Fatigue Re-Assessment of Marine Structures". 37th International Conference on Ocean, Offshore and Arctic Engineering. American Society of Mechanical Engineers. doi:10.1115/OMAE2018-77915. ISBN 978-0-7918-5120-3. Unknown parameter
|s2cid=
ignored (help) - ↑ Glaessgen, Edward H.; Stargel, D.S. (April 2012). "The Digital Twin Paradigm for Future NASA and U.S. Air Force Vehicles". 53rd AIAA/ASME/ASCE/AHS/ASC Structures, Structural Dynamics and Materials Conference 20th AIAA/ASME/AHS Adaptive Structures Conference 14th AIAA. doi:10.2514/6.2012-1818. hdl:2060/20120008178. ISBN 978-1-60086-937-2.
- ↑ Iglesias, Daniel; Bunting, Patrick; Esquembri, Sergio; Hollocombe, Jonathan; Silburn, Scott; Vitton-mea, Livio; Balboa, Itziar; Huber, Alexander; Matthews, Guy F.; Riccardo, Valeria; Rimini, Fernanda; Valcarcel, Daniel (December 2017). "Digital twin applications for the JET divertor". Fusion Engineering and Design. 125 (125): 71–76. doi:10.1016/j.fusengdes.2017.10.012.
- ↑ Lund, Arnold M.; Mochel, Karl; Lin, Jeng-Weei; Onetto, Raimundo; Srinivasan, Jayanthi; Gregg, Peter; Bergman, Jeffrey Eric; Hartling, jr., Kenneth D.; Ahmed, Anwar; Chotai, Sham (21 March 2016). "Digital Wind Farm System" (PDF).
- ↑ Shah, Tapan; Govindappa, Suresh; Nistler, Paul; Narayanan, Babu (22 February 2017). "Digital Twin System for a Cooling System" (PDF).
- ↑ General Electrics. "Digital Twin Framework". Retrieved 22 May 2020.
- ↑ Bosch. "Bosch IoT Device Management". Retrieved 22 May 2020.
- ↑ Grieves, Michael (19 April 2007). Product Lifecycle Management: Driving the Next Generation of Lean Thinking. pp. 278–280. Search this book on
- ↑ Wagg, D.J.; Worden, Keith; Barthorpe, Robert; Gardner, Paul (March 2020). "Digital Twins: State-of-The-Art Future Directions for Modelling and Simulation in Engineering Dynamics Applications". ASCE-ASME J Risk and Uncert in Engrg Sys Part B Mech Engrg. 6 (3). doi:10.1115/1.4046739. Unknown parameter
|s2cid=
ignored (help) - ↑ Schlesinger, S.; Crosbie, R.E.; Gagné, R.; Innis, G.S.; Lalwani, C.S.; Loch, J.; Sylvester, R.J.; Wright, R.; Kheir, N.; Bartos, D. (1979). "Terminology for Model Credibility". Simulation. 32 (3): 103–104. doi:10.1177/003754977903200304. Unknown parameter
|s2cid=
ignored (help) - ↑ Min, Qingfei; Lu, Yangguang; Liu, Zhiyong; Su, Chao; Wang, Bo (December 2019). "Machine Learning based Digital Twin Framework for Production Optimization in Petrochemical Industry". International Journal of Information Management. 49: 502–519. doi:10.1016/j.ijinfomgt.2019.05.020. Unknown parameter
|s2cid=
ignored (help) - ↑ Alexopoulos, Kosmas; Nikolakis, Nikolaos; Chryssolouris, George (220). "Digital twin-driven supervised machine learning for the development of artificial intelligence applications in manufacturing". International Journal of Computer Integrated Manufacturing. 33 (5): 429–439. doi:10.1080/0951192X.2020.1747642. Unknown parameter
|s2cid=
ignored (help) - ↑ Sakaridis, Christos; Dai, Dengxin; van Gool, Luc (September 2018). "Semantic Foggy Scene Understanding with Synthetic Data". International Journal of Computer Vision. 126 (973–992): 973–992. arXiv:1708.07819. doi:10.1007/s11263-018-1072-8. Unknown parameter
|s2cid=
ignored (help) - ↑ Ruiz, Nataniel; Schulter, Samuel; Chandraker, Manmohan (2019). "Learning To Simulate". International Conference on Learning Representations (ICLR). arXiv:1810.02513.
- ↑ Busoniu, Lucian; Babuska, Robert; De Schutter, Bart; Ernst, Damien (April 2010). Reinforcement Learning and Dynamic Programming Using Function Approximators. CRC Press, Inc. ISBN 978-1-4398-2108-4. Search this book on
- ↑ Rasheed, Adil; San, Omer; Tvamsdal, Trond (October 2019). "A. Rasheed, O. San and T. Kvamsdal, "Digital Twin: Values, Challenges and Enablers," 2019".
- ↑ Rochetta, R.; Bellani, L.; Compare, M.; Zio, E.; Patelli, E. (1 May 2019). "A reinforcement learning framework for optimal operation and maintenance of power grids". Applied Energy. 241: 291–301. doi:10.1016/j.apenergy.2019.03.027. hdl:11311/1122896. Unknown parameter
|s2cid=
ignored (help) - ↑ Silver, David; Huang, Aja; Maddison, Chris J.; Guez, Arthur; Sifre, Laurent; van den Driessche, George; Schrittwieser, Julian; Antonoglou, Ioannis; Panneershevam, Veda; Lanctot, Marc; Dieleman, Sander; Grewe, Dominik; Nham, John; Kalchbrenner, Nal; Sutskever, Ilya; Lillicrap, Timothy; Leach, Madeleine; Kavukcuoglu, Koray; Graepel, Thore; Hassabis, Demis (27 January 2016). "Mastering the game of Go with deep neural networks and tree search". Nature. 529 (7587): 484–489. Bibcode:2016Natur.529..484S. doi:10.1038/nature16961. PMID 26819042. Unknown parameter
|s2cid=
ignored (help) - ↑ Kamthe, Sanket; Deisenroth, Marc Peter (9–11 April 2018). "Data-Efficient Reinforcement Learning with Probabilistic Model Predictive Control" (PDF). 21st International Conference on Artificial Intelligence and Statistics (AISTATS 2018). Lanzarote, Canary Islands, Spain. 84. arXiv:1706.06491.CS1 maint: Date format (link)
External links[edit]
- Public website of the ITEA4 ASIMOV project
- ITEA4 Website
- ASIMOV Project Page on the ITEA4 website
- Eureka website
This article "ITEA4 ASIMOV Project" is from Wikipedia. The list of its authors can be seen in its historical and/or the page Edithistory:ITEA4 ASIMOV Project. Articles copied from Draft Namespace on Wikipedia could be seen on the Draft Namespace of Wikipedia and not main one.